No tiene artículos en su carrito de compras.
Antes de que se conviertan en un elemento único de las calles de una ciudad abarrotada, las tapas de alcantarilla tienen que pasar por un complejo proceso de producción. Desde el diseño del patrón hasta el vertido del hierro fundido, la fabricación de las tapas de alcantarilla es una tarea increíblemente laboriosa pero fascinante que implica paciencia, preparación e incluso un toque de creatividad.
Puede que las tapas de alcantarilla tengan el deber de mantener la seguridad de los peatones, pero los trabajadores de la fábrica tienen la responsabilidad aún mayor de garantizar que estos discos de hierro fundido sean lo suficientemente fuertes como para soportar las duras condiciones y el peso de los vehículos. Si tiene curiosidad, veamos cómo se fabrican las tapas de alcantarilla.
El proceso de fabricación
Las tapas de pozo de hierro fundido suelen fabricarse mediante un proceso de moldeado en arena en fábricas conocidas como fundiciones. El proceso de fundición consta de los cuatro pasos siguientes:
Elaboración del patrón
Las tapas de alcantarilla suelen tener algún tipo de motivo o imagen que puede representar la cultura de una ciudad o la expresión de un artista. En la mayoría de los casos, los moldes de tapas de alcantarilla se tallan en madera o se crean en aluminio con una máquina.
Cada tapa de alcantarilla requiere dos diseños: uno para la parte superior que mira hacia arriba y otro para la parte inferior. La parte superior suele tener un diseño más decorativo, mientras que la parte inferior suele ser plana. A veces, la parte inferior presenta un diseño, como un dibujo de telaraña tridimensional. Esto proporciona una mayor resistencia sin aumentar el peso de la tapa de alcantarilla.
Preparación del molde
Para empezar el proceso de moldeo, se colocan dos mitades del modelo de pozo en cajas conocidas como "matraces". La arena verde -arena húmeda (a veces mezclada con arcilla, aceite o resina) que aún no ha fraguado y que, por tanto, está todavía en estado "verde"- se introduce apretadamente en estos frascos para crear los moldes. Este proceso se conoce como moldeo en arena.
Cuando se retiran los patrones, quedan impresas en la arena las imágenes huecas de las mitades superior e inferior de la tapa de alcantarilla. Estas mitades pueden entonces ensamblarse en un gran marco metálico, también conocido como "frasco de arrastre".
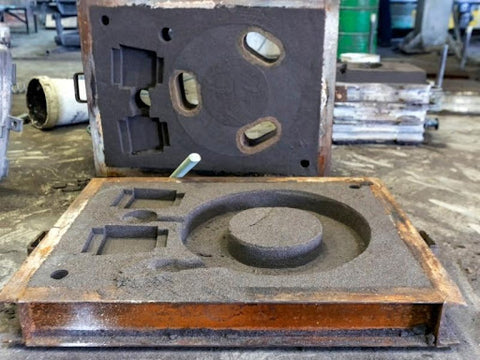
Fundir y verter
En una fundición, la chatarra puede fundirse en distintos tipos de hornos para crear una tapa de alcantarilla. Dependiendo del metal, la fusión suele producirse a unos 2.300 - 2.700 grados Fahrenheit. A continuación, se pueden alear (mezclar) otros metales con el hierro fundido para aumentar su resistencia o aglutinar impurezas. Esta unión crea un producto de desecho llamado "escoria" que flota en la parte superior del hierro fundido para ser eliminado.
Los trabajadores de la fundición utilizan un gran cazo o caldero de metal para recoger el hierro fundido y verterlo en el molde de arena a través de los agujeros de la mufla, conocidos como bandas. Otros agujeros sirven de respiraderos que permiten la salida de los gases. A medida que la fundición de hierro se enfría, los trabajadores deben vigilar que no salgan gases del molde y asegurarse de que no queden atrapados en su interior, lo que provocaría burbujas no deseadas en la fundición.
Enfriamiento y acabado
Normalmente, el hierro fundido se enfría ligeramente después de una hora y media, lo suficiente para que los trabajadores de la fundición puedan retirar los moldes. El hierro tarda aproximadamente un día en enfriarse por completo. Una vez terminado el enfriamiento, los trabajadores de la fundición retiran la arena con un cepillo de alambre o colocando la pieza fundida enfriada en una rejilla vibratoria.
En la fase de acabado, se elimina el exceso de metal que se ha endurecido en la cámara de colada, conocido como bebedero. Como paso final, se puede granallar la superficie. Esto ayuda a garantizar que la tapa de alcantarilla sea antideslizante, no se oxide y quede completamente plana dentro de su marco.
¿Cómo será la producción de pozos en el futuro?
Aunque el hierro fundido es muy económico, otros materiales para las tapas de alcantarilla, como el acero, el plástico y el material compuesto, son habituales en entornos singulares. Los ordenadores pueden incluso desempeñar un papel en el futuro de las tapas de alcantarilla en la creación de diseños y la fabricación asistida por ordenador, denominada CAD-CAM. Esta tecnología permite a los diseñadores de tapas de alcantarilla cortar sus patrones a partir de moldes de plástico mediante máquinas automáticas. Este proceso tardará sólo unos minutos en fabricar una tapa de alcantarilla.
Aunque el futuro de la fabricación de tapas de alcantarilla parece prometedor, las tapas de alcantarilla actuales son igual de interesantes. Para más información sobre la fabricación de tapas de alcantarilla, consulte nuestra entrada del blog en la que explicamos qué hace que una tapa de alcantarilla sea tan pesada.